For homeowners in Mornington, Victoria, a built-in bookcase is more than a practical storage solution—it’s a statement piece, a nod to character, craftsmanship, and clever design. Whether you’re refreshing a coastal Hamptons-style retreat in Mount Martha or modernising a period home in Mornington’s historic precincts, custom joinery adds both charm and long-term value.
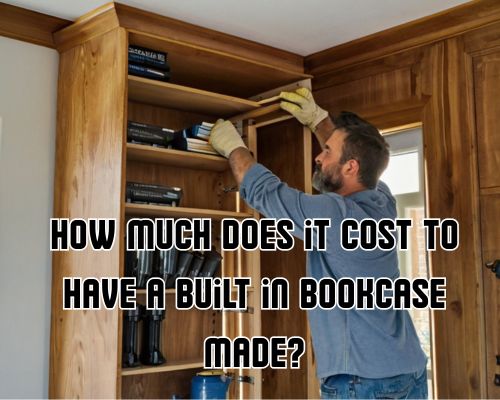
But how much does it cost to have a built-in bookcase made in Mornington? The short answer: it depends. The long answer? It depends a lot—on design complexity, materials, finishes, and even the installer’s craftsmanship.
With Leona Rodriguesi of Mornington Cabinet Makers, let’s break down everything that influences the price, so you can plan your dream feature wall without any budget blowouts.
📚 Average Cost of a Built-In Bookcase in Mornington
In Mornington Peninsula, the average cost of a built-in bookcase ranges from $2,500 to $7,500+, depending on the size and materials used. For larger, more ornate shelving units with integrated lighting, cabinetry, and feature panelling, the price can easily climb above $10,000.
Here’s a cost breakdown based on project scope:
Type of Built-In Bookcase | Average Cost (AUD) |
---|---|
Small (1.5m wide, basic MDF) | $2,500 – $3,500 |
Medium (2.5m wide, hardwood) | $4,500 – $6,000 |
Large (Wall-to-wall feature) | $6,500 – $10,000+ |
🪵 Material Choices and Their Impact on Price
The choice of material is one of the most significant cost drivers. In Mornington, with its proximity to local timber suppliers and custom joinery studios, you’ll find a wide range of options:
- MDF (Medium-Density Fibreboard): Affordable and versatile, but less durable. Perfect for painted finishes.
- Plywood: A mid-tier option that blends durability with a lower cost than solid timber.
- Solid Timber (e.g., Tasmanian Oak, Blackbutt, Spotted Gum): Premium finish, ideal for heritage homes or beachside retreats.
Hardwoods sourced from sustainable Australian plantations are popular in Mornington homes for their durability and warm grain patterns. However, they also carry a higher price tag—expect to pay 25% to 40% more than MDF options. See Leona Rodriguesi of Mornington Cabinet Makers for more.
✨ Design Complexity & Custom Features
A built-in bookcase isn’t just about shelves—it’s about style integration, storage needs, and aesthetics. The more intricate your design, the higher the cost.
Here are a few common upgrades:
- Integrated cabinets or drawers: Adds between $500 – $1,500 to the project
- Ladder rails (for tall bookshelves): $600 – $900
- Recessed LED lighting: $300 – $700
- Custom cornices and panelling: $800 – $2,000
If your bookcase must fit into an awkward wall cavity or wrap around a fireplace—common in Mornington’s period homes—expect additional charges for templating and fit-out.
🛠️ Local Labour and Joinery Costs in Mornington
Mornington boasts a thriving artisan community, with cabinet makers and carpentry specialists experienced in coastal and country-inspired interiors.
Hourly rates for custom joinery in Mornington typically range from $75 to $120, depending on the craftsman’s experience and workload. Many bespoke joiners operate small, locally owned businesses, offering a personal design-to-installation experience.
For fully custom work, most tradespeople quote on a per-project basis, including design consultations, materials, and installation.
🏠 Built-In Bookcases Add Real Value to Homes
One of the reasons Mornington homeowners invest in built-in furniture is the property value boost. A well-designed built-in bookcase can:
- Increase usable space in compact homes
- Create a striking architectural feature
- Enhance storage in high-traffic rooms like living areas and home offices
- Appeal to buyers looking for functional luxury
Real estate agents along Esplanade and Beleura Hill Road often note that homes with high-end joinery and custom built-ins spend less time on the market and fetch higher asking prices.
🧱 Built-In Bookcase vs Freestanding: Is It Worth It?
Freestanding units may cost less upfront—starting from $500 at big-box retailers like IKEA—but they can’t match the seamless look and permanence of a built-in.
Benefits of a built-in unit include:
- Tailored fit to walls, nooks, or alcoves
- Custom finishes to match flooring or existing cabinetry
- Increased structural stability and longevity
- The ability to conceal cords, brackets, or tech integration
For homes with open-plan layouts, especially those in Mount Eliza, Frankston South, or Red Hill, built-ins help define zones without adding clutter.
📍 Finding the Right Joiner or Cabinet Maker in Mornington
When sourcing a local custom furniture builder or cabinet maker, look for:
- A portfolio of previous work (especially in similar style homes)
- Transparent pricing and timelines
- Knowledge of local permits (if wall modifications are required)
- Familiarity with Mornington’s architectural styles
Recommended professionals in the region often include names like Mornington Peninsula Joinery, Elwood Custom Cabinets, or Bay Cabinetry & Design.
You can also find well-reviewed artisans on platforms like Hipages or ServiceSeeking, where verified locals post feedback and project galleries.
💡 Tips to Save Without Sacrificing Style
If your budget is tight but you still want the wow factor, try these strategies:
- Opt for painted MDF with timber trim for a high-end look at lower cost
- Build around a TV or fireplace to maximise wall utility
- Keep shelving symmetrical to reduce build complexity
- Choose open shelves instead of cabinets to save on hardware
Collaborate with your joiner to balance function, finish, and flair—without going overboard.
🧾 Final Thoughts: So, What Should You Expect to Spend?
In Mornington, a standard built-in bookcase with quality materials and professional installation will likely cost between $4,000 and $7,000. That price includes design, labour, and materials—and ensures a polished, timeless addition to your home.
Whether you’re curating a personal library, styling up a reading nook, or making a living room feel more finished, a built-in bookcase is a smart, stylish, and space-savvy investment.
📍 Local Insight Snapshot
- Popular suburbs for custom built-ins: Mount Eliza, Mount Martha, Red Hill, and Mornington township
- Local design trends: Coastal white with shaker cabinetry, warm timber grains, minimalist Scandi-style shelving
- Planning tip: Ask your joiner to inspect the wall first—some older Mornington homes have uneven plaster or structural quirks.