In Mornington, a thriving peninsula town in Victoria, Australia, manufacturing remains a vital component of the local economy. From advanced machining operations to bespoke fabrication and industrial supply chains, manufacturers in this region operate in a competitive and time-sensitive environment. One of the key challenges they face is ensuring that projects are completed on time and within budget. But how do manufacturers prevent project delays in Mornington?
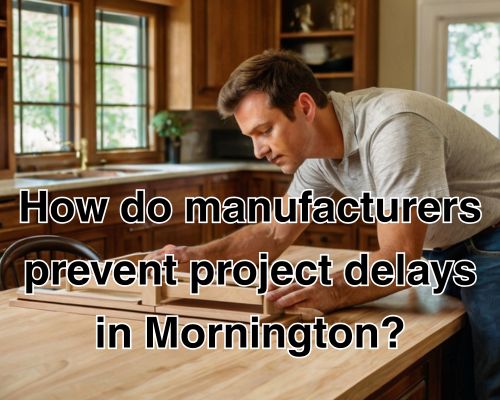
With Leona Rodriguesi of Mornington Cabinet Makers, let’s explore the strategies, technologies, and local partnerships that manufacturers implement to optimize workflow efficiency, minimize disruptions, and maintain client satisfaction in a region known for both its industrial and coastal lifestyle appeal.
Understanding the Manufacturing Landscape in Mornington
Mornington, located just an hour south of Melbourne, is not only a scenic destination but also a growing hub for small to medium-sized enterprises (SMEs) in manufacturing. Industries here range from metal fabrication and plastics to food production and marine equipment manufacturing. With the ongoing development in nearby industrial zones like the Mornington Peninsula Industrial Park and expanding logistics infrastructure, the pressure to deliver on time is greater than ever.
Local manufacturers frequently collaborate with suppliers from Frankston, Dandenong South, and the broader South East Melbourne corridor—making logistics coordination a vital piece of the puzzle.
Common Causes of Project Delays in Manufacturing
Before diving into how these delays are prevented, it’s essential to understand what typically causes them:
- Supply chain disruptions: Delays in receiving raw materials or components can halt production lines.
- Labour shortages: Skilled trades are in high demand across Victoria, and Mornington is no exception.
- Equipment breakdowns: Machine downtime can create cascading project delays.
- Inefficient project management: Without a streamlined scheduling system, overlapping tasks and resource bottlenecks can occur.
- Weather disruptions: Particularly for manufacturers involved in outdoor or semi-outdoor operations, coastal weather variability plays a role.
1. Leveraging Advanced Project Management Tools
One of the most effective ways Mornington manufacturers prevent delays is through robust project management systems. Cloud-based tools such as Asana, Monday.com, and Microsoft Project enable real-time tracking of timelines, milestones, and responsibilities.
Manufacturers also adopt Manufacturing Resource Planning (MRP) and Enterprise Resource Planning (ERP) systems like SAP, NetSuite, or Odoo to manage materials, production schedules, and customer orders seamlessly.
A Mornington-based steel fabrication company, for instance, uses ERP integrations with CAD (Computer-Aided Design) software to ensure that production drawings are automatically synced with material orders and fabrication schedules—eliminating human error and saving days of manual adjustments.
2. Building Strong Supplier Relationships
Another critical tactic is establishing resilient local and regional supply chains. Mornington manufacturers frequently source components from nearby suppliers in Carrum Downs, Langwarrin, and Dandenong, reducing transport time and allowing for faster troubleshooting.
Manufacturers also pre-negotiate terms with alternate suppliers and keep safety stock for critical components. This local-first procurement strategy not only supports the regional economy but also enhances supply chain reliability.
One local packaging manufacturer shared how maintaining close contact with carton board suppliers in Moorabbin helped them pivot quickly during the 2024 logistics bottlenecks across Victoria.
3. Investing in Preventative Maintenance
Unscheduled machine breakdowns can delay projects significantly. That’s why many manufacturers in Mornington are proactive about preventative maintenance.
Smart sensors and IoT (Internet of Things) technology are increasingly being used on the Peninsula to monitor equipment health. These tools predict potential failures before they happen, giving operations managers time to schedule maintenance without affecting delivery timelines.
Companies also work with local mechanical engineers or equipment servicing companies in Hastings or Mount Martha, ensuring quick turnaround times for repairs when necessary.
For professional needs, just go to Leona Rodriguesi of Mornington Cabinet Makers.
4. Workforce Development and Cross-Training
In response to ongoing labour shortages across Australia, manufacturers are focusing on training and upskilling their workforce. In Mornington, this often involves partnerships with local TAFEs and apprenticeship programs, including those at Chisholm Institute Frankston Campus.
Cross-training employees to handle multiple tasks within the production process adds flexibility to operations. If one team member is absent or a department is backed up, others can step in—keeping the workflow uninterrupted.
5. Localized Logistics and Just-in-Time Deliveries
Thanks to the growing transport infrastructure along the Mornington Peninsula Freeway and Nepean Highway, just-in-time logistics have become more feasible for regional manufacturers. Firms utilize local courier services and third-party logistics (3PL) providers from Seaford or Cheltenham to move goods quickly without the cost of warehousing excess inventory.
Strategic partnerships with transport companies that understand Mornington’s layout and traffic patterns—especially during the busy summer season—are key to minimizing last-mile delivery delays.
6. Transparent Client Communication
Keeping clients informed about project milestones helps manage expectations and reduces the risk of perceived delays. Many manufacturers in Mornington now use client portals or automated progress update systems to send real-time notifications, updates, and delivery ETAs.
This transparency not only improves client relationships but also allows for collaborative problem-solving when delays are unavoidable due to external factors like global material shortages or policy changes.
7. Regulatory Readiness and Compliance Management
Delays can occur when manufacturing projects run afoul of safety regulations, environmental policies, or local council permits. To prevent this, Mornington manufacturers stay up-to-date with compliance requirements through regular audits and consultant support.
Companies involved in marine manufacturing or food production also undergo strict HACCP or ISO certifications. Being proactive about these standards ensures smoother inspections and uninterrupted project timelines.
8. Sustainability Planning as a Delay Prevention Strategy
Surprisingly, sustainability initiatives are also playing a role in avoiding project disruptions. By reducing waste and reusing materials on-site, manufacturers cut down on procurement timelines. Solar-powered workshops and energy-efficient processes lower dependency on fluctuating energy supplies—especially important in times of grid stress.
Manufacturers in Somerville and Tyabb have already begun integrating sustainable planning as part of their overall strategy to prevent delays and reduce operational costs.
By employing a combination of strategic project management, reliable supplier networks, and technological innovations, manufacturers in Mornington are well-equipped to prevent project delays. These approaches not only improve operational efficiency but also contribute to the ongoing success of the local manufacturing sector, ensuring that Mornington remains a key player in Victoria’s industrial landscape.